False Brinelling Test Rig
False brinelling damages can occur in rolling bearings if a stationary bearing is subjected to dynamic loads and/or pivot movements with very small amplitudes. The dynamic loads and very small pivot movements can be generated, for example, by machine and unit vibrations, but also during the transport of machines or vehicles by road, rail, and ship are generated.
False brinelling damages can occur in rolling bearings if a stationary bearing is subjected to dynamic loads and/or pivot movements with very small amplitudes. The dynamic loads and very small pivot movements can be generated, for example, by machine and unit vibrations, but also during the transport of machines or vehicles by road, rail, and ship are generated. False brinelling has the potential to significantly reduce the service lifetime of these components. In addition, false brinelling damages can result in increased noise emissions, negatively impacting the performance of machines.
False brinelling causes relative movements of the contact partners in the Hertzian contact zone, which leads to damage to the surfaces of the rolling elements and rolling bearing rings.
Measures to reduce dynamic loads and micromovements are often very costly and cannot always reduce false brinelling damages to the desired extent. More effective and economical is the use of lubricants that can specifically prevent the formation of false brinelling damages.
with false brinelling damages
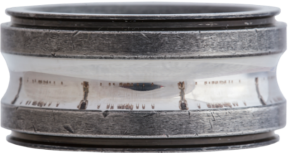
(low, medium and severe)
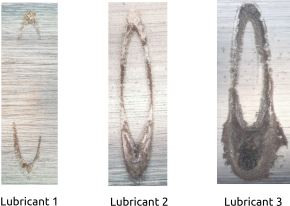
Our modern false brinelling test rig and the test methods and evaluation criteria used are well established in the industry and are used to evaluate lubricants and investigate the influence of operating conditions on false brinelling damages.
Experience and a large number of investigations show that the development of false brinelling damages is more pronounced at low temperatures. For investigations at lower temperatures, the false brinelling test rig can be operated fully automated in a climate chamber.
- Testing of angular contact ball and tapered roller bearings, optionally deep groove ball bearings
- oscillating and rotating operation
- axial dynamic load
- radial dynamic load
- test temperature +40 °C ... -40 °C
- preconfigured and arbitrarily definable test conditions
- operation via touchscreen
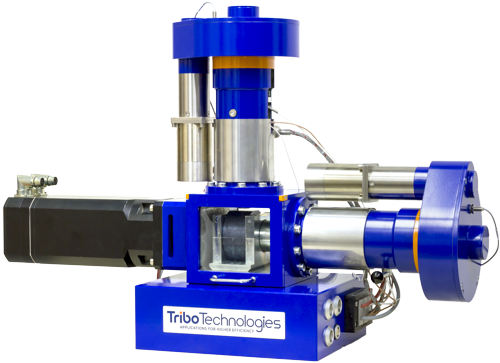
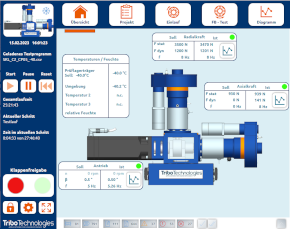
The corrosive attack, the wear volume and the wear depth have proven themselves for evaluating false brinelling damages. With our Wear Analyzer software, false brinelling marks can be evaluated in terms of wear volume, material application and wear depth.
- automated calculation of wear and application volume excluding surface roughness
- direct analysis of 3D surface scans: cropping, unwinding of the curved macro geometry and filtering
- automated processing of multiple surface scans possible
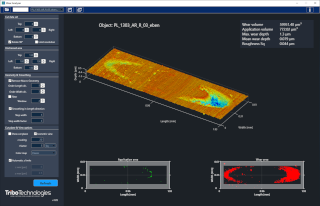
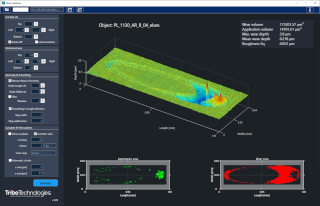
Are you interested in a false brinelling test rig or are you looking for an experienced partner for testing and evaluating your lubricants?
Here you can contact us.
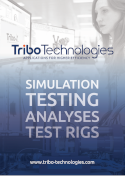